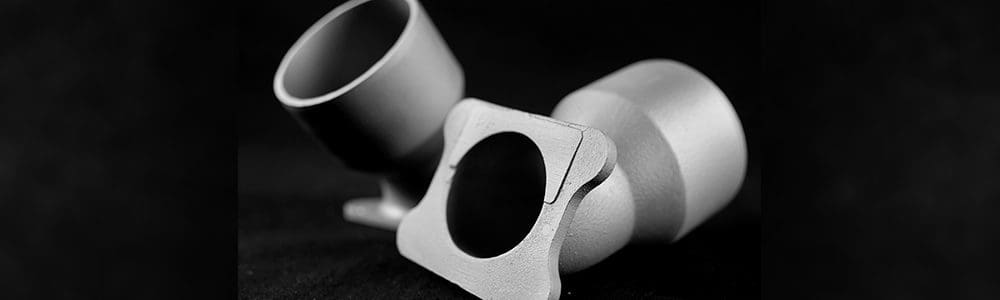
Guide to Investment Casting With Nickel Alloys
Investment casting is a process that uses expendable wax or 3D printed stereolithography patterns in the shape of the casted metal part. The patterns are then overlaid with a ceramic refractory coating to form a mold. The patterns are melted out of the molds leaving a cavity for the pouring of metals including aluminum, stainless steel, cobalt, or nickel.
In this month’s article, we’ll cover why nickel alloys are sometimes used in investment casting, the most common types of nickel alloys, and the most common industry applications of nickel alloy castings.
Why Nickel Alloys?
Nickel is a metal with excellent corrosion and oxidation resistance at high temperatures. It is relatively easy to alloy nickel with other materials like iron, copper, chromium, molybdenum, titanium, and others. Casting with nickel alloy will produce a finished part that can withstand extremely harsh environments.
Nickel alloys also retain their high hardness value while maintaining their superior weldability and ductility. Their ability to withstand high temperatures, coupled with strong chemical corrosion, heat, and stress corrosion resistance, make nickel-based alloys the go-to casting material for aerospace, defense, energy, chemical, and automotive applications.
Most Common Types of Nickel Alloys
There are three major types of nickel alloys that are typically used during the investment casting process: Monel®, Inconel®, and Hastelloy. We’ll cover each type in more detail in the sections below.
Monel®
Monel® is a nickel-based alloy consisting primarily of nickel (approximately 70%), copper (approximately 20%), iron, and manganese (approximately 5%) with trace elements of other metals. It has excellent machining properties, high strength, and excellent corrosion resistance. It’s a material used in the oil and gas industry for hydrocarbon processing equipment like pumps, valves, fittings, etc.
Inconel®
Next, Inconel® is a material that maintains its mechanical and chemical properties at high temperatures. This makes it an ideal material for jet engines and other aerospace applications where high heat resistance is critical to operation. The material also has high tensile and yield strength while having excellent impact resistance and fatigue strength. These alloys often combine nickel, chrome, iron, titanium, and molybdenum.
Hastelloy®
Lastly, Hastelloy® is another material with excellent weldability, chemical corrosion resistance, and stress corrosion resistance. It’s an alloy made of nickel, chrome, and molybdenum. Much like Inconel®, it has high tensile and yield strength. Capable of withstanding high temperatures, this material won’t lose any of its ductility, which makes it an excellent material for highly corrosive environments.
Industry Applications
The nickel alloys mentioned above are primarily used to create investment castings for aerospace, medical, and defense applications.
Within aerospace, these heat-resistant nickel-alloys are essential for jet engines and jet engine components, turbine blades, aerofoils, and turbine casings. They are highly valued for their hardness, excellent adhesion, corrosion protection and strength.
In the medical industry, these materials are used to manufacture medical instruments, orthopedic implants, surgical tools, and other medical devices. They are often the preferred material for ensuring the high sterility of medical devices.
Lastly, the defense and military industries use these materials for aircraft components and military equipment. Among other applications, nickel alloys are used in communication, electrical equipment, aircraft and jet components, missiles, defense systems, and rockets.
Have Questions? Contact Barron Industries Today!
Barron Industries has a long and storied history within the metal casting industry that goes back to 1983. Our metallurgists, engineers, technicians, and operators have the required skills, training, expertise, and experience needed to design and manufacture cutting-edge nickel alloy investment castings.
Please contact us today if you have any questions about nickel alloys and how they’re used during the casting process, or if you’re interested in a quote.