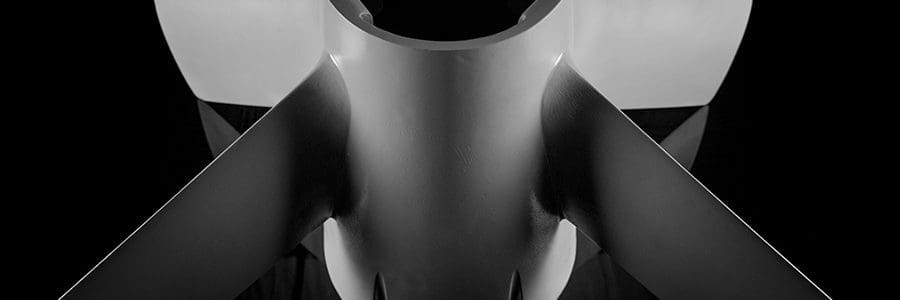
Everything You Need to Know About Aerospace Castings
Precision is crucial in the aerospace industry. Parts must be strong but lightweight, and all designs must comply with rigorous standards and regulations. The production process must also be quick enough to accommodate supplier needs. You may be thinking “how can high-quality parts be made fast enough?” The answer is simple: aerospace casting.
In this article, we’ll cover a popular casting technique used to produce high-quality parts in the aerospace industry.
What is Casting?
Casting is a manufacturing process in which molten metal is poured into a mold of a desired shape and allowed to solidify. This process is widely used because it provides precise results while reducing waste. Manufacturers typically rely on casting to mass produce simple to complex parts that must be able to withstand harsh conditions and ranging pressures.
Although there are different types of casting processes, the one known as investment casting, or the lost wax process, is a popular method for aerospace components.
How Does Aerospace Casting Work?
Aerospace industries rely on the investment casting process for the manufacture of complex thin-walled and lightweight components. The name investment casting is derived from the pattern being “invested” or surrounded with a refractory material. The technique employs a mold formed around a wax pattern, which eventually melts away, to create the finalized part, which can weigh anywhere from a few ounces to several hundred pounds. Aerospace casting is also known as the lost wax or precision casting process as high-strength castings can be mass produced with fine detail and strict tolerance requirements, reducing the need for machining and other secondary finishing. Common aerospace casting alloys include:
- A356 & A357 Aluminum
- Inconel 600 & 625
- HastelloyA & Hastelloy X Nickel-based Alloy
- 17-4 & 15-5 PH Stainless Steel
- 347 Austenitic Stainless Steel
- 410 & 421 Marensitic Stainless Steel
- Cobalt 6, Cobalt 21 & Cobalt 31 family of alloys
Benefits of Aerospace Castings
There are many benefits associated with aerospace castings including the flexibility in choice of materials. An investment casting can be produced using many different alloy compositions including aluminum, stainless steel, carbon steel and nickel-based alloys. In addition to producing parts of intricate shapes and sizes, investment casting also helps minimize material waste and conserve energy. It also provides manufacturers the ability to cast complex parts with superb surface finishes, greater dimensional accuracy and no flash or parting lines. But one of the greatest benefits is the ability to convert expensive multi-part fabrications into a single-piece aerospace casting. This greatly reduces manufacturing cost and delivery times.
Protecting Our Environment
Investment Casting is one of the greenest manufacturing methods; in fact, it is primarily a recycling process that uses no hazardous materials and produces no hazardous waste. Aerospace casting companies use recycled wax to produce patterns, and when the wax is melted out of the ceramic molds, it is collected for reuse. Although the ceramic shell material cannot be recycled within the investment casting process, it is classified as an inert substance and controlled landfill disposal is not necessary. Waste from ceramic slurry can also be recycled for many uses including fill for construction projects or filler for concrete.
Casting Aerospace Components
There are many components that can be manufactured using aerospace casting, including a wide range of engine and fuel system parts.
Many non-engine components are also cast for aerospace applications. Cabin control systems, hydraulic systems parts, environmental controls, landing systems, and other internal mechanical parts can be effectively and economically created using high-quality casting.
These levels of variability and adaptability account for the reason why casting has remained popular as a manufacturing option for most aerospace applications. By delivering superior results at a lower cost, casting offers significant savings without compromising the quality of the components needed for aircraft production.
Why Choose Barron Industries for Aerospace Investment Casting?
Founded in 1923, Barron Industries has nearly a century’s worth of experience. Over the years, we’ve grown into a full-service, AS 9100- and Nadcap Accredited global manufacturer. We offer everything from initial part design and rapid prototypes to CNC machining, assembly and non-destructive testing.
Our complete turnkey manufacturing process ensures the delivery of high-quality, mission-critical components with reduced lead-times. Utilizing our manufacturing software, we track your part all the way through the process, from initial design to final quality control checks and testing. Our top priority is ensuring quality every step of the way.
If you’re interested in learning more about our extensive aerospace casting experience, click here to read our case study.
Call Barron Industries Today
We specialize in both rapid prototype and precision castings, and can help with any aerospace application. Learn more about our casting capabilities, or contact us online to request a quote.